Reverse Osmosis and Ultra filtration systems
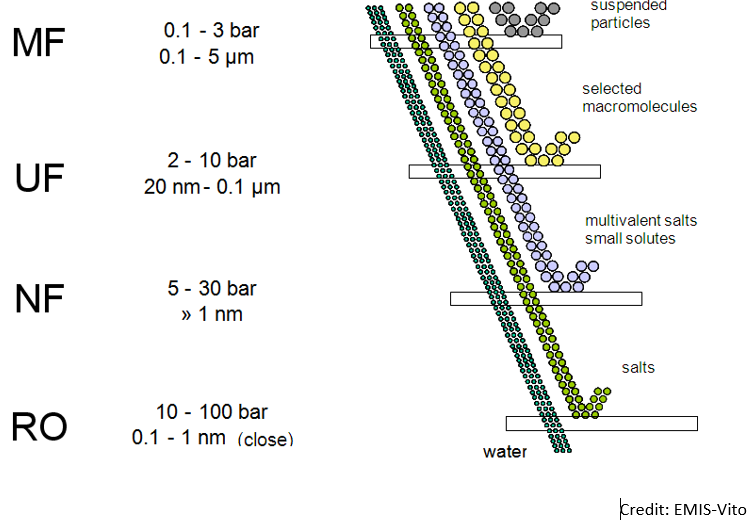
Operating a reverse osmosis (RO) plant involves several significant costs, which can vary depending on the plant’s size, location, and specific technology and membranes used.
Costs and challenges involved in the operation of an RO plant:
Energy Consumption: Energy costs are often the largest operational expense for RO plants. The process requires high-pressure pumps to force water through semi-permeable membranes, which can be energy-intensive, particularly for seawater desalination.
Membrane Replacement and Maintenance: The semi-permeable membranes used in RO systems are subject to fouling and degradation and must be replaced periodically. Maintenance also includes cleaning and repairing these membranes to ensure efficiency and longevity.
Chemicals for Treatment: Pre-treatment and post-treatment chemicals are necessary to condition the water before and after the RO process. This might include anti-scalants to prevent scale buildup, biocides to control biological growth, and pH adjusters. The costs of these chemicals can be significant.
Labor: Skilled operators and maintenance personnel are essential for the efficient running of an RO plant. Labor costs can vary widely by location but typically represent a significant portion of operational expenses.
Disposal of Brine: The disposal of concentrate or brine (highly concentrated salt water produced as a byproduct of RO) can be costly, especially if special handling, transportation, or treatment is required to meet environmental regulations.
Plant Infrastructure Maintenance: Ongoing maintenance of the plant infrastructure, including pumps, pipes, valves, and control systems, is crucial for operation and can be costly, particularly as equipment ages.
Water Source and Quality: The quality of the feed water significantly impacts costs; poorer quality feed water requires more extensive pre-treatment and more frequent membrane cleaning and replacement, thus increasing operational costs.
Operating an ultrafiltration (UF) plant involves several key cost elements. Although similar in some ways to reverse osmosis (RO), ultrafiltration typically deals with larger particles and therefore has its own unique operational cost profile.
Costs and challenges involved in the operation of a UF installation:
Membrane Replacement and Maintenance: Like RO, the membranes in UF systems are crucial and can be expensive. They require regular cleaning to prevent fouling and must be replaced when they become too worn or damaged to function effectively. Maintenance also includes ensuring that the integrity of the membranes is maintained to prevent bypass or leakage of untreated water.
Energy Consumption: Although UF requires less pressure than RO, energy costs can still be significant, especially for large-scale installations. Energy is primarily used to pump water through the membranes and for backwashing (reversing the flow to clean the membranes).
Chemicals for Cleaning and Pre-treatment: Chemicals are used for the cleaning of membranes and sometimes for the pre-treatment of water to remove materials that could foul the membranes. These might include coagulants, flocculants, and biocides. The types and amounts of chemicals required depend largely on the quality of the feed water.
Labor Costs: Skilled labor is necessary for monitoring and maintaining the UF system. This includes routine checks, troubleshooting, repairs, and general system management. Labor costs vary depending on local wage rates and the level of automation within the plant.
Disposal of Waste Streams: UF systems produce waste streams from backwashing and membrane cleaning. The handling and disposal of these waste streams can incur costs, especially if they must be treated before disposal due to environmental regulations.
Infrastructure Maintenance: Ongoing maintenance of the system’s physical infrastructure, such as pumps, valves, and control systems, is required to keep the plant operational and efficient.
System Downtime and Reliability: Operational inefficiencies, breakdowns, and system downtime can lead to significant costs, both in terms of lost production and the expenses associated with repairs and replacements.
By combining innovative and environmentally friendly products and technologies we can:
Help with the pre-treatment, keep the membranes clean, reduce the backflushing frequency and consequently:
- reduce chemicals consumption (acidic/alkaline/detergents/surfactants/disinfectants/biocides/chelating agents/…)
- increase the flux
- increasing the lifespan of the membranes
- reduce manual cleaning intervals and save material and labor costs.